You might ask “IS IT POSSIBLE TO APPLY PRINT DESIGNS ON GLASS”? I would say “Absolutely”.
It may come as a revelation, but silk screen printing on glass is a highly prevalent technique in the packaging industry. Whether you’re looking to add a simple single color or a vibrant multi-color design, both options are achievable. Dive into this blog post where the lesser-known advantages of silk screen printing on glass are unveiled, and the entire process is meticulously broken down.
What Is Silkscreen Printing on Glass Bottles?
Silk screen printing on glass bottles is a decorative and branding technique that involves pressing ink through a stenciled mesh screen to create a printed design on the surface of the bottle. This method is particularly popular for producing intricate logos, texts, and images directly on the glass. This technique has been widely adopted in the perfume industry to create visually appealing and unique packaging.
Silk screen-printed glass refers to a float glass decorated by screen printing. For the application of frit during screen printing, three different patterns are used:
- Dots
- Lines
- Empty gaps or across the whole surface
The end product can be transparent, translucent or opaque. However, it depends upon which technique is used. Combining a large range of basic glass and various colors gives the makers a big room for creativity.
What Is the Process of Silkscreen Printing on Glass Bottles?
The process of silkscreen printing on glass bottles involves several steps to ensure a high-quality and durable result. Here is a brief overview of the process:
- Design Creation: The desired design is created using specialized software or hand-drawn on a transparent film. This design will serve as the template for the silkscreen printing process.
- Screen Preparation: A mesh screen is selected based on the complexity of the design. The screen is coated with a light-sensitive emulsion and then dried in a darkroom.
- Glass Bottles Preparation: The glass bottles are thoroughly cleaned and dried to remove any dust or contaminants that could affect the adhesion of the ink.
- Ink Application: The screen is aligned over the glass item, and ink is placed on top of the screen. A squeegee is used to press the ink through the open areas of the stencil onto the glass surface. Only the areas of the screen that were washed out during development will allow ink to pass through.
- Drying and Curing: The printed glass is then passed through a drying tunnel or curing process, which may involve heat or UV light to ensure the ink sets properly on the glass, allowing the ink to adhere to the surface of the glass. This ensures a long-lasting and vibrant design.
Any Limitations When Designs Are Made for Printing on Glass Bottles?
Silk screen printing on glass bottles allows for vibrant colors and effects that can be more durable and scratch-resistant than traditional labels. It gives the bottles a premium feel, often associated with high-quality products, and adds a layer of brand recognition and aesthetic appeal. However, there are some limitations should be considered regarding the design and size are made?
Obstacles You May Face In Screen Printing on Glass Surface
Typical Advantages of Silkscreen Printing on Perfume Glass Bottles
1. Durability: Silkscreen printing on glass bottles provides a durable and long-lasting design. The ink bonds with the glass surface, making it resistant to fading, scratching, and washing. Unlike labels, they won’t come off over time or when exposed to moisture or friction during handling and shipping.
2. Vibrant Colors: Silkscreen printing allows for vibrant and opaque colors to be applied to glass bottles. This can create eye-catching designs that stand out on store shelves.
3. Brand Customization: Silkscreen printing offers a high level of customization, allowing brands to create unique designs that reflect their brand identity. This can help differentiate their products from competitors and enhance brand recognition. Brands can create a customer tailored range of perfumes. Customers can share their font and color ideas with the vendor. Customized products are always in huge demand. Customers are always willing to pay more for the product that matches their demand and desires exactly.
4. Versatility: Silkscreen printing allows for a broad range of vibrant colors and special effects, including metallic, frosted, or textured finishes that may not be possible with conventional labels. It can be applied to various shapes and sizes of glass bottles, making it a versatile option for different product lines. It can be used on both flat and curved surfaces, allowing for creative and visually appealing designs.
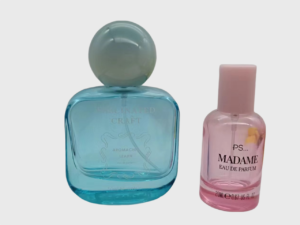
You must have heard that “first impression is the last impression.” When customers see a product for the first time, the product packaging makes the first impression. You might lose a customer if the product packaging is not done right.
It would be best to make your product unique to stand out from your competitors. Customers are more informed to prefer style and creativity these days. Therefore, unique packaging and printing can greatly impact consumers’ purchase intentions.
Screen printing on glass is not only just a unique way of communicating brand identity, but it is also a unique finish and a creative look to the product. You can make use of as many colors as you want. You can use unique colors and techniques to make the printing more creative. These techniques include glow-in-the-dark and precious metals. Customers assess the quality of the product through its packaging.
In Conclusion, silkscreen printing on glass bottles is a valuable technique in the perfume industry, allowing brands to create visually stunning packaging that captures the essence of their products. It allows for vibrant colors and effects that can be more durable and scratch-resistant than traditional labels. It gives the bottles a premium feel, often associated with high-quality products, and adds a layer of brand recognition and aesthetic appeal, which make it a popular choice for many perfume manufacturers.